The Importance of Stainless Steel Finish in Precision Engineering
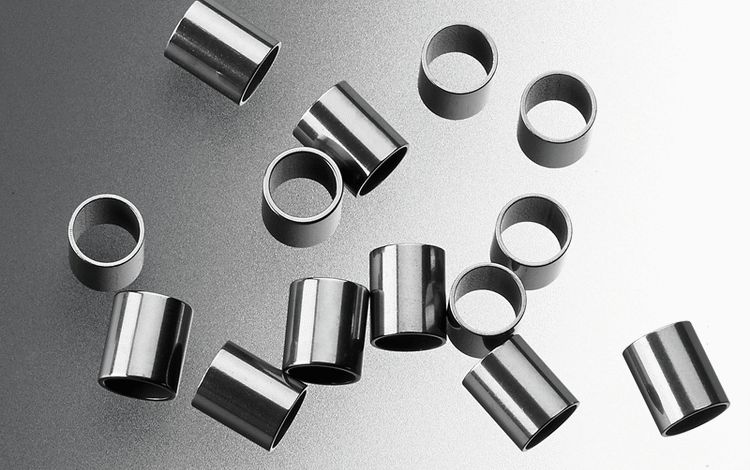
Why Stainless Steel Finishes Matter
Surface finishing techniques can significantly impact regulatory approval and remediation efforts in sectors like saltwater-exposed applications, steam cleaning, and chemical exposure. Tailoring the finishing technique to project needs ensures reliability, safety, and efficiency, making it a crucial investment in healthcare and chemical plants.
Stainless steel’s strength and corrosion resistance are enhanced by its surface finishing, particularly in precision engineering. The chosen finish enhances equipment’s functionality, sanitization speed, and compliance with regulatory requirements and contributes to its longevity. For example, facilities focusing on cleanroom environments or food manufacturing lines depend on specific finishes to limit contamination and simplify sterilization. When opting for a solution like 316L stainless steel, users benefit from an optimal mix of corrosion resistance and surface smoothness, making it a go-to material for both industrial and medical contexts where the margin for error is virtually zero.
Common Stainless Steel Finishes Explained
The world of stainless steel finishes is diverse, with options like brushed, matte, satin, and mirror-polished surfaces. The finishing technique significantly impacts the metal’s appearance, texture, and usability. Brushed finishes are popular in kitchens, elevators, and architectural features. In contrast, mirror-polished finishes offer high reflectivity and a smooth surface. Specific finishes impact structural performance, such as corrosion resistance, ease of cleaning, and minor abrasions. Satin finishes provide a subtle gleam and camouflage minor scratches, while matte finishes are utilitarian and require less maintenance. Understanding these distinctions helps engineers and contractors exceed performance expectations.
Matching Finishes to Project Requirements
Selecting the right stainless steel finish is crucial in various industries, such as food and beverage, medical, heavy machinery manufacturing, and aerospace. Polished finishes help maintain sanitation, while ground finishes allow parts to withstand high-velocity contact, vibration, or extreme thermal cycling. In food and beverage, polished finishes reduce contamination risk and speed up cleaning cycles. Brushed steel combines a sleek, modern appearance with practicality, while ground finishes provide optimal surface contact for mating components. In industrial tools, turned and polished bars support precision tolerances and reduce friction. Collaborating with materials engineers early in the design or renovation process ensures functional success and regulatory harmony.
Benefits of Turned, Ground, and Polished Stainless Steel
Turned, ground, and polished stainless steel (TGP) is a popular choice for precision projects. This finishing process produces a smooth, true-to-size product, ideal for applications requiring flawless rotation, precise sliding fit, or minimal friction. The turning stage eliminates surface deformities, the grinding stage refines roundness, and polishing perfects the final finish, resulting in a lustrous appearance and greater corrosion resistance. TGP stainless steel is essential for drive shafts, piston rods, linear motion assemblies, and surgical implements. Its longevity and performance help mitigate field failures and reduce total lifecycle costs. It also reduces the risk of pitting and microbiological contamination.
Industry Standards and Testing
Stainless steel finishes are based on globally recognized standards and rigorous quality control testing. These standards cover various aspects, including roughness averages, permissible surface flaws, and dimensional tolerances. Adherence to these standards is crucial for organizations in highly regulated markets like healthcare or aviation. Verification often involves advanced equipment, such as digital surface profilometers, salt-spray, and chemical resistance tests, to reduce variability and ensure long-term performance.
Caring for Stainless Steel Surfaces
The lifespan of stainless steel is directly linked to its treatment during daily use. Regular cleaning with gentle detergents, warm water, and soft cloths removes surface pollutants and biological debris, ensuring corrosion resistance. Avoid abrasive pads or harsh chemicals for highly polished or TGP finishes. Clean surfaces regularly, using non-abrasive cleaning agents, and conduct periodic inspections to prevent costly repairs. Consistent care preserves aesthetics, protects investment, and supports regulatory compliance in sectors like healthcare and hospitality.
Final Thoughts on Stainless Steel Finishes
Stainless steel’s well-earned reputation for resilience and beauty depends on thoughtful finishing choices at each step of an engineering project. Engineers and decision-makers ensure long-term savings and consistent regulatory compliance by carefully aligning finish properties with site-specific needs. Today’s material science knowledge, coupled with robust industry standards and real-world data, enables smarter finish choices—no matter how challenging the environment or complex the operational demands. Ultimately, a well-chosen finish transforms stainless steel from a commodity material into a key driver for reliable, high-performance systems and safer, longer-lasting products.